Making fiber optic cable is both simple and complex. The simplicity is in heating the glass to melting and drawing it out. The complexity is in the composition of the glass and which materials (minerals and elements) are added to that glass to make it the ideal medium for light. Be sure to refer to the video at the end of this article for a full demonstration.

How Fiber Optic Cable is Made
by LiamBean
There's some interesting science that goes into the making of fiber optic cable. Some of it is materials science or how certain minerals function; other aspects involve physics.
Introduction
Overview
This article will discuss how fiber-optic cable is made. In the process of explaining it the article will also cover the different types of fiber-optic cable including Single-Mode and Multi-Mode fiber. And even the different types of Multi-Mode fiber.
From Fiber Optic Communications an Overview, Mode refers to the wavelength of light. As the names imply single-mode fiber supports only one wavelength, multi-mode supports many different wavelengths of light.
Single Mode and Multi-Mode
Single mode is voice for distance; multi-mode for voice, Internet, and TV
As stated above single-mode fiber-optic cable is designed to carry a single wavelength of light. Multi-mode fiber is designed to carry multiple wavelengths of light.
There have been many versions of multi-mode fiber over the years. All of which are directly defined by the way the fiber is manufactured to begin with.
Multi-mode fiber was initially a large core (sixty-two point five microns) and multiple wavelengths of light were "shot" down it. Typically the light going down the core followed a straight line, bounced off of the cladding at short distances, or bounced off of the cladding farther down the fiber. All of this was determined by the angle at which the light entered the cable.
Step Index Multi-mode Cable
Multi-mode cable designed for multiple bandwidths of light is/was called "step-index" fiber. It is designed to allow the beams of light to travel straight down the core (rare) or bounce from one side of the core to the other (common) as the light beam traverses the cable. This cable was typically "doped1" with germanium, boron, and titanium. All of these elements are suspended in a gas, deposited inside the tube of pure silica glass, then heated until they fuse with the glass. As the glass tube is drawn down a core if formed with these elemental additives making up part of the core.
Graded Index Multi-mode Cable
Another type of multi-mode cable is called "graded index" cable and it made in a similar fashion to the "step index" cable except that the inner core is created in many more steps with every step having slightly more concentrations of the elemental gases mentioned above. These are added to create a core with with more "dopants" added in the center and fewer on the outside of the core. What this process does is force the light approaching the outside of the core to curve back in toward the center of the core. This manufacturing technique has allowed for the creation of fiber that can carry light signals up to four times farther than step-index muli-mode cable.
Laser Optimized Multi-mode Cable
A newer type of cable is being created which is also graded index, but includes the element Erbium along with titanium, boron, and gallium. Erbium has a unique property in that it fluoresces (glows) at certain wavelengths of light. As luck would have it Erbium tends to fluoresces at exactly the wavelengths required for fiber-optic communications. This type of fiber-optic cable is called "laser optimized."
Singlemode Cable
Single mode also now includes the dopant Erbium in its makeup much like the laser optimized cable mentioned above. Unlike the multi-mode cables above multi-mode typically has more steps in the manufacturing process devoted to creating the cladding layer rather than the core.
Effects of Core Structure
As the reader can see from the third image at right the different fiber types handle the light beam sent down it differently. In the step-index cored cable the light bounces from the center to the cladding and back in toward the core. In the graded index the light "bends" back in toward the core. In the single-mode fiber the light tends to stay down the center of the core.
The input and output pulses should give the reader a good indication of how light is affected as it travels from one end to the other of various types of fiber-optic cable.
![]() | Fiber Optics Technician's Manual FIBER OPTICS TECHNICIAN'S MANUAL, 4E is the ideal practical guide for designers, installers, and troubleshooters of fiber optic cable plants and networks. It reflects recent cha... |
![]() | Fiber-Optic Communication Systems (Wiley Series in Microwave and Optical Engineering) This book provides a comprehensive account of fiber-optic communication systems. The 3rd edition of this book is used worldwide as a textbook in many universities. This 4th edit... |
How the Fiber Cable is Formed
The process described here is more or less the same regardless of cable type. The only differences are in the number of steps and the dopants added to the core prior to forming.
- A purified glass tube is acquired or created from ultra pure silicon glass. The tube is roughly three feet long.
- The tube is immersed in an acid bath to remove any impurities.
- The tube is allowed to dry.
- The tube is then placed in a lathe like fixture and heated. The heating torch is moved from one end of the tube to another while elemental gasses are introduced through one of the openings.
- The tube is then heated further until the gases deposit on the inner walls of the tube forming a thin powder. These elemental gases may be a combination of gallium, titanium, boron, and/or erbium.
- The heating process is intensified the length of the tube (by moving the torch from one end to the other) fusing the elemental soot to the glass.
Steps five and six may be repeated a number of times to form a graded or laser optimized core. - The tube is then heated further until it just becomes malleable. The tube is then pulled from both ends until the inner area closes in upon itself. This forms the core.
- The newly formed rod is separated from the tube and transferred to the fiber drawing tower.
- The free end of the rod is carefully passed through a furnace at the top of the tower. As the furnace heats the glass rod it is naturally drawn down through the furnace by gravity; this forms the fiber.
- The free end of the fiber is passed through a laser micrometer. This insures that the diameter of the fiber remains consistent as it is drawn.
- The free end of the fiber is then passed further through two UV plastic coating stages. These stages coat the fiber with plastic and cure it with ultraviolet light.
- The first UV coating is flexible.
- The second UV coating is less flexible and is there to protect the glass from rough conditions.
- The coated fiber is then passed through an idler wheel and tensioner. This insures the fiber is drawn at a consistent speed.
- The coated fiber is then transferred to a take up spool.
- The entire drawing process is monitored by computer from beginning to end. The speed of the take up spool is regulated by this computer.
The speed of the tensioner and take-up spool directly controls the diameter of the cable.
Once the cable is formed additional color coded sheathing is typically added for ease of use during installation. This sheathing is called the buffer.
Coda
As the reader can see most of the work in creating the fiber goes into the quality of the materials and the inner "impurities" introduced to the glass tube prior to it being drawn. Threading the drawn fiber is pretty straight-forward in comparison, with a strong assist from computers controlling the process of pulling the fiber.
As methods and practices have been standardized creating the fiber cable has become cheaper and cheaper.
You might also like
History of Iron WorksIron has been in use since prehistoric times dating back to 4000 BCE. That is...
Stationery An Inclusive IndustryFor an industry to be successful it has to be inclusive. Modern businesses em...
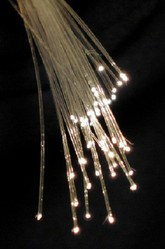
Comments