Safety can be seen retroactively. Our measurements have already occurred, our injuries already taken place. What we measure has already happened.
How can we find ways to manage so that we don't get measurements?
Done right we don't have injury measurements for our Safety.
How can we keep improving Safety if we get zero injuries?

Safety + Measure = Manage
by Fargy
How we measure effects how we manage Safety. What we measure does and when. Perhaps more importantly though is Why.
We are what we measure.
How we look at measurements defines how we look at a problem.
Years ago a steelworks I worked at had a Key Performance Indicator of 10 Lost Time Injuries a month. A Lost Time Injury, or LTI, meant the employee left the site during a shift.
So if an employee spent the rest of the shift in the medical centre it was not a Lost Time Injury.
The first 8 or so Lost Time Injuries did not have the same urgency as the 9th or 10th when it might be taken up at a management meeting. Managers did not like breaking injury records.
If it was near the end of the month and we didn't have 10 Lost Time Injuries, employees would jokingly refer to needing a few volunteers to meet the target.
The culture was one that can be found in any dangerous workplace. In this instance it was the idea that Steelworks are dangerous places, that injuries were part of the job. Except that the deaths and injuries were occurring from crushing, falls and electrical shock, rather than burn injuries.
Injuries were thought to be commonplace because it was a Steelworks, therefore injuries became commonplace.
The other systems that effected measurement and management of Safety were; a reward culture for production targets based on steel created on a shift supervisor basis.
Combined with a strong blame and fault culture, what happened was shifts would compete with other shifts. The honesty of reports became suspect.
What was being measured was not what was happening. So management was always going to be impossible.
Lost Time Injury Frequency Rate.
LTIFRs are our most popular Safety indicator.
We have LTIFR as a measurement to compare our progress.
It is the amount of Lost Time Injuries (of a full day, excluding fatalities) divided by the number of hours worked.
To get a million hour LTIFR then multiply LTIs by 1,000,000 and then divide by number of hours worked.
This standard measurement is used to compare businesses against each other, or parts of a business against others.
LTIFR is used to measure how badly we fail. If an organisation has LTIFRs as the pinnacle of their measurement systems, then their system fails.
LTIFRs fail to give a real indication of what is going on. One does not gain an idea of how long the Lost Time Injuries were for. 10 LTI's of a month each has the same value as 10 LTI's of a day each. Yet the first is closer to achieving fatalities.
Hours worked can include different plants in the same organisation. With varying mixes of heavy industry and office workers the same hours worked with the same LTIs can mean vastly different things.
If you see LTIFRs without a deeper explanation, then they are a superficial measurement, indicating a shallow perspective on how to measure and manage Safety.
![]() | DEWALT DPG82-11C Concealer Clear Anti-Fog Dual Mold Safety Goggle The Concealer is a dual mold goggle that provides extra fog control and ventilation with an impact resistant lens. Its dual-injected rubber provides a soft, comfortable seal, wh... |
![]() | Steps to Safety Culture Excellence Provides a clear road map to instilling a culture of safety excellence in any organizationDid you know that accidental injury is among the top ten leading causes of death in eve... |
![]() | MSA Safety Works NFL Hard Hat, Chicago Bears The most popular sport in America is football, and MSA Safety Works NFL Hard Hats give fans a distinctive way to show their team loyalty. These licensed NFL hard hats meet OSHA ... |
![]() | MCR Safety N9674XL Ninja X Nylon/Spandex Shell Gloves with Bi-Polymer Dipped Palm and Fingertips,... Premium durability and softness complement a bi-polymer coating on palm and fingertips for solid protection. These high-performance gloves are treated with Actifresh® to kill ba... |
What to measure.
What effects each organisation is different.
One thing that effects all organisations is change.
So measure change, manage change.
Do you audit when conditions change at your workplace?
Here are some common workplace changes that all organisations have.
Weather. Have you thought about how weather effects your workplace?
Day/Night cycle. Have you thought about how shift work effects your workplace?
These two factors cover physiological changes in employees and a whole gamut of other side issues. For example snowing at night when using a vehicle outdoors. Compared to summer driving in a sudden downpour.
These are variables common to all organisations. Everyone should know how rain and other factors effect their organisation and its safety.
If one wants to tailor a specific list for one's own organisation one can enlarge that list by measuring the changes that the organisation is subject to.
For examples, legislative safety changes effect each organisation differently. Production schedules effect each organisation differently.
Measuring Almosts.
Safety management involves thousands of variables.
Some accidents may only ever happen once through a combination of variables that are highly unlikely to ever sequence that way again.
So making rules up to cover every single accident that happened in the past and hoping people remember the rule when, or if, it should happen again is not the way forward.
What we could also measure are the almosts. The near misses. The clues that we get before someone gets injured.
Doing that is an automatic part of group meetings held just before a new task. You will hear people assess risk and outline their thoughts on what could go wrong. They are measuring the almosts.
Safety. Measuring, what happened, is doing it wrong, people have been hurt then.
Find a way to measure possibilities and keep doing that, because those possibilities change every day. With the weather and the time of day, with changing production schedules and different experience levels of employees on the next shift.
It is possible to be safe from injury.
If you don't believe that, you will be measuring injuries. If you want your organisation to be successful for year after year, then manage safety by measuring. But manage what you measure, tailor it for your organisation.
Safety management is about eliminating risks, which does the same as production management which is about eliminating waste and excess steps. But Safety is more forward looking so use that framework.
Measure what you can think to measure. So that you don't have to measure failures.
Other article by same author.
You might also like
First Aid: Would you Know What to Do?A medical emergency could happen at any moment. The question is whether you h...
Piriformis - an unusual form of sciaticaOnly 10% of the population have their sciatic nerve pass through their pirifo...
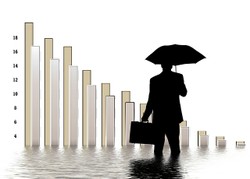
Comments